average training hours per employee
Sustainability
Building a better future today
At Sacyr, we are aware of our role as a driver of change in society, with sustainability as a fundamental pillar of our activities.
We focus our ESG vision on those areas where the organization can have the greatest impact, in terms of the environment (circular economy, climate change, natural capital, water, sustainable cities), social (people and communities) and governance (ethics and human rights, transparency, innovation, sustainable finance, risk management).
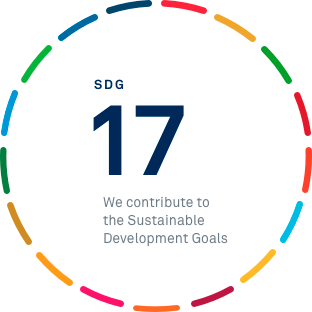
€M in distributed economic value
waste recycled, reused or recovered
of STEM women in the workforce
Innovation
We envision solutions
We shape our ideas to make them a reality. We transform our environment with talent and vigor. We foster a culture of innovation and encourage an open-model work method to drive change.
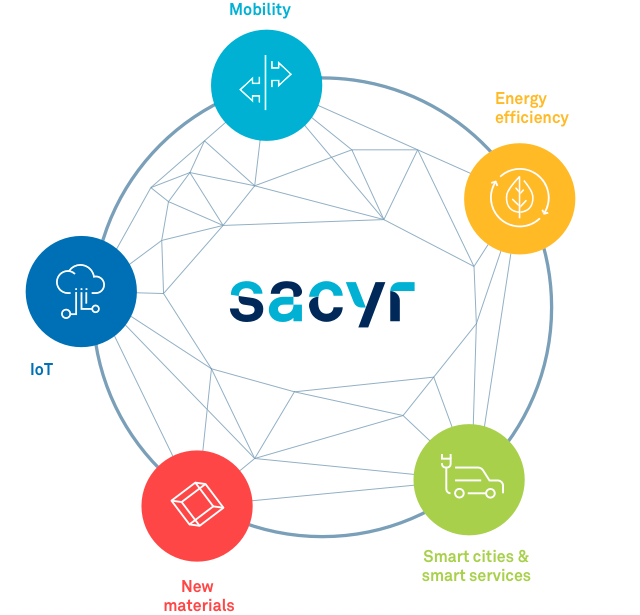
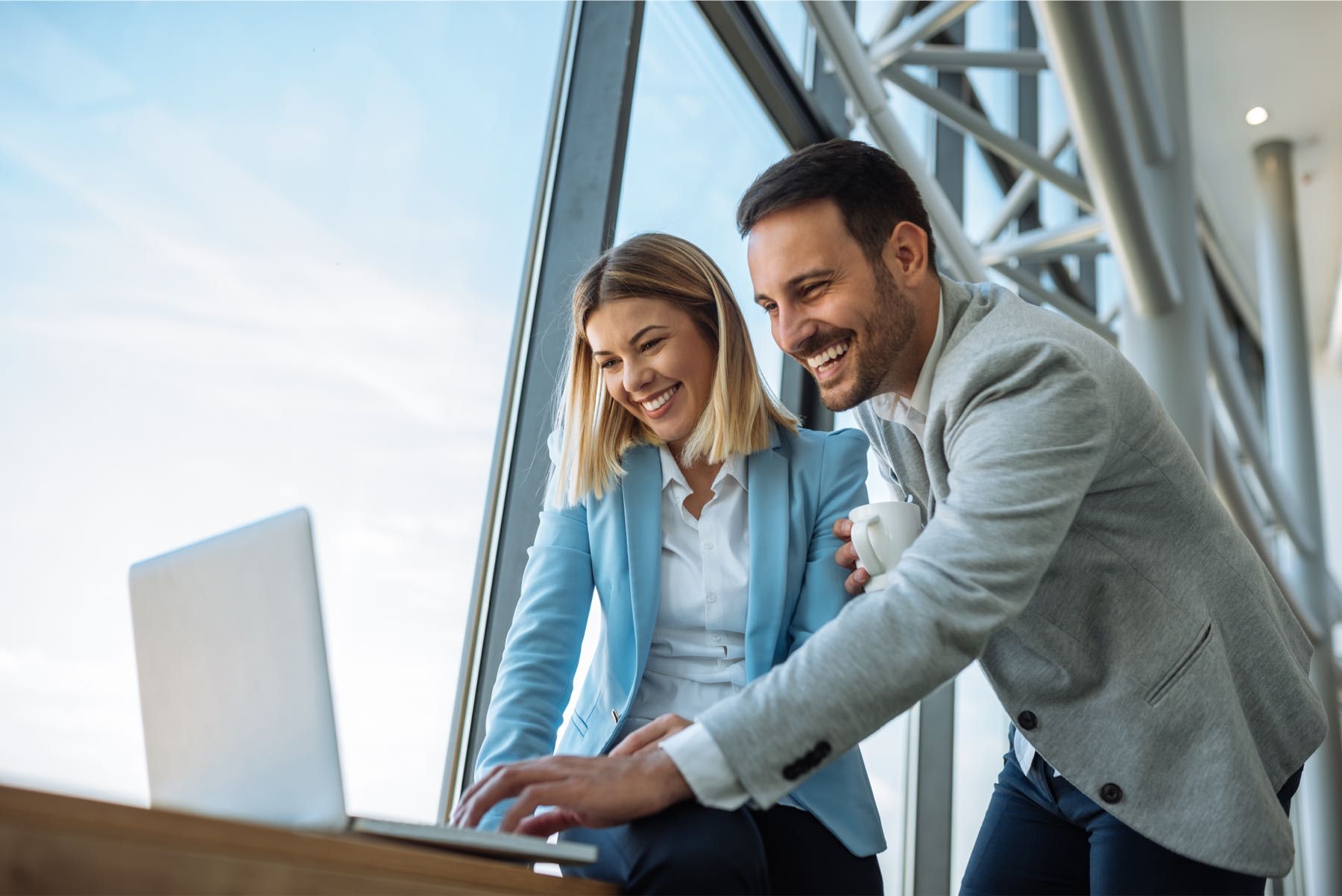
Develop your career at Sacyr
People are the key to our success. Learn more about our coordinates and join the team!